Mastering Aluminum Coil Handling: A Comprehensive Guide to Tilters and Upenders
Handling large, heavy aluminum coils presents significant challenges in metal fabrication, processing, and logistics. Manual manipulation is often impractical and poses safety risks. This is where specialized material handling equipment, specifically aluminum coil tilters and upenders, becomes essential. These machines are designed to safely and efficiently rotate or tilt heavy coils, typically by 90 degrees, transitioning them between eye-to-wall (horizontal axis) and eye-to-sky (vertical axis) orientations for subsequent processing, storage, or transport.
This guide provides an in-depth look at aluminum coil tilters and upenders, covering their operation, benefits, key features, and crucial safety considerations, aligning with the practical needs of the modern fabricator.
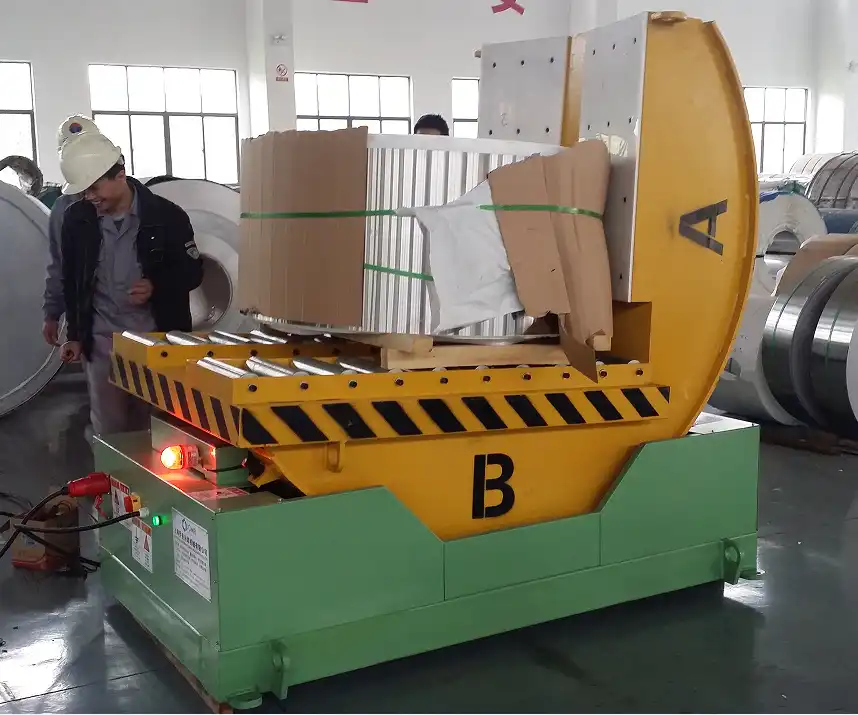
Why Use Aluminum Coil Tilters and Upenders?
Integrating coil tilting equipment into your workflow offers several key advantages:
- Enhanced Safety: Significantly reduces the risk of injuries associated with manually handling heavy or awkwardly positioned coils. Prevents potential crushing hazards.
- Improved Efficiency: Speeds up the coil repositioning process compared to manual methods or less specialized equipment, minimizing downtime between operations.
- Material Protection: Gentle and controlled movement prevents damage, such as denting or scratching, to sensitive aluminum surfaces during rotation.
- Process Integration: Facilitates smooth transitions between different stages, such as loading onto decoilers, placing into storage racks, or preparing for shipment.
- Versatility: Handles a wide range of coil sizes and weights, adaptable to various production requirements.
Understanding the Mechanics: How Coil Tilters Work
While designs vary, most aluminum coil tilters and upenders share fundamental components:
- Heavy-Duty Frame: Provides a stable base, typically constructed from robust steel, designed to withstand the forces involved in tilting heavy loads.
- Coil Cradle: The platform or structure that securely supports the coil during the tilting operation. Cradles often feature a V-shape or flat surface, sometimes with protective padding (like high-density polyurethane) to prevent coil damage. They may be adjustable to accommodate different coil diameters and widths.
- Tilting Mechanism: The system responsible for rotating the cradle. Common types include:
- Hydraulic Systems: Offer high power density, suitable for very heavy coils, providing smooth and controlled motion.
- Electro-Mechanical Systems: Utilize electric motors and gear reducers, offering precise control and often requiring less maintenance than hydraulics.
- Manual/Assisted Systems: Occasionally used for lighter coils, employing cranks or levers, sometimes with mechanical advantages.
The core function involves rotating the cradle, and the coil it holds, between horizontal and vertical orientations (or vice-versa) reliably and safely.
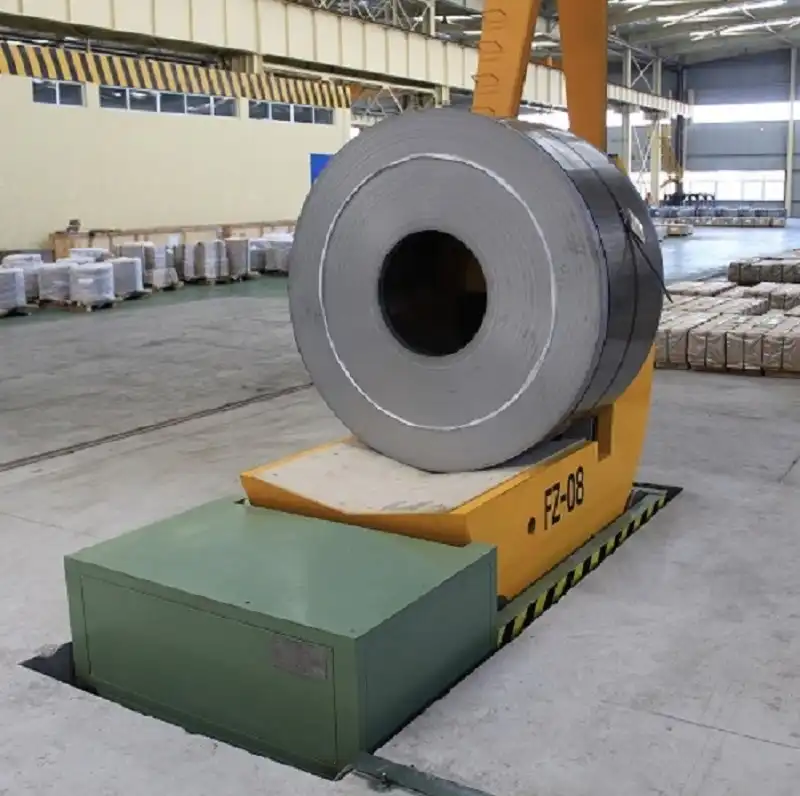
Key Features and Considerations When Selecting Equipment
Choosing the right coil tilter involves evaluating several factors:
- Load Capacity: Must exceed the maximum weight of the coils you handle.
- Coil Dimensions: Ensure the cradle can accommodate your range of coil widths, inner diameters (ID), and outer diameters (OD).
- Tilting Angle: Typically 90 degrees, but verify if specific intermediate angles are needed.
- Cycle Time: How quickly the machine can complete a tilting operation, impacting overall throughput.
- Control System: Options range from simple push-button pendants to more sophisticated PLC (Programmable Logic Controller) integration for automated lines.
- Safety Features: Essential elements include:
- Limit Switches: Prevent over-travel of the tilting mechanism.
- Safety Guards/Barriers: Protect personnel from moving parts.
- Emergency Stops: Immediately halt operation in critical situations.
- Load Holding Valves (Hydraulic Systems): Prevent accidental lowering in case of power loss.
- Interlocks: May prevent operation unless safety gates are closed or the coil is properly positioned.
- Footprint and Layout: Consider the space required for the machine and safe operating zones within your facility.
Applications Across the Industry
Aluminum coil tilters are indispensable in various operational contexts:
- Receiving and Warehousing: Tilting incoming coils for proper storage on pallets or racking systems.
- Feeding Processing Lines: Positioning coils correctly (eye-to-sky) for feeding into slitting lines, cut-to-length lines, stamping presses, or roll forming machines.
- Loading and Unloading: Safely manipulating coils during transfer to/from trucks, railcars, or other transport methods.
- Inter-Process Handling: Repositioning coils between different manufacturing stages.
Essential Safety Practices for Operation and Maintenance
Safe operation is paramount when working with heavy coil handling equipment. Adherence to strict safety protocols is non-negotiable:
- Operator Training: Only trained and authorized personnel should operate coil tilters. Training must cover machine-specific controls, load limits, emergency procedures, and potential hazards.
- Personal Protective Equipment (PPE): Operators must wear appropriate PPE, including safety glasses, steel-toed boots, and gloves. Hard hats may be necessary depending on the environment.
- Pre-Operation Checks: Conduct daily inspections to ensure the machine is in good working order, checking controls, safety features, hydraulic lines (if applicable), and structural integrity.
- Load Capacity Adherence: Never exceed the manufacturer's specified maximum load capacity. Ensure the coil is centered and stable within the cradle before initiating the tilt.
- Clear Operating Zone: Maintain a clear area around the tilter during operation, ensuring no personnel are within the swing radius or potential drop zone.
- Regular Maintenance: Follow the manufacturer's recommended maintenance schedule for lubrication, inspection of wear parts, and system checks. Document all maintenance activities.
- Lockout/Tagout (LOTO): Implement strict LOTO procedures during maintenance and repair work to prevent accidental machine startup.
For comprehensive guidelines on material handling safety, consult resources from organizations like the Occupational Safety and Health Administration (OSHA).
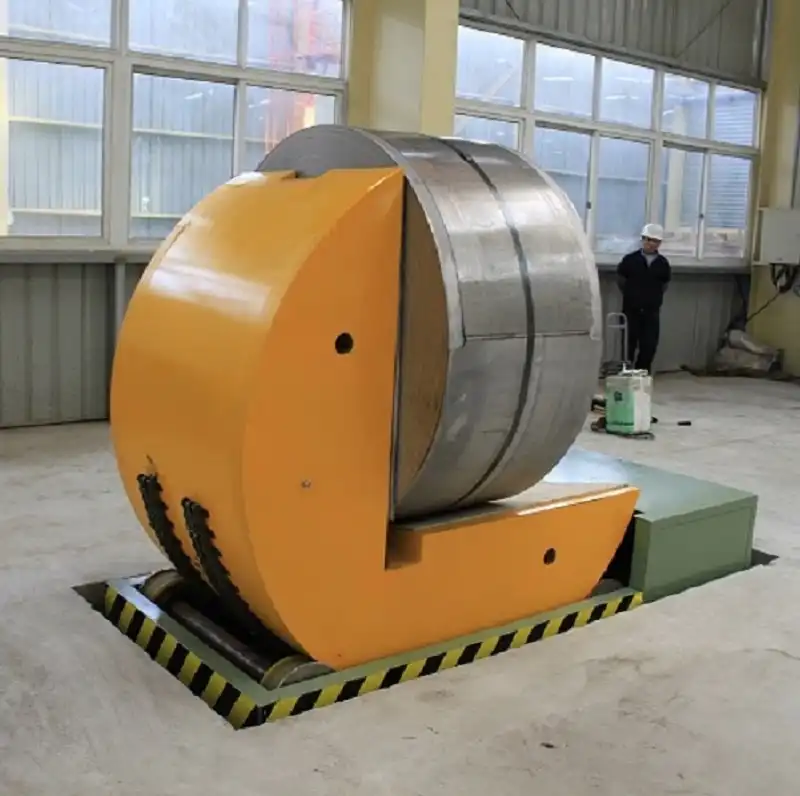
Conclusion
Aluminum coil tilters and upenders are vital tools in modern metal fabrication and processing environments. They provide a safe, efficient, and reliable method for manipulating heavy aluminum coils, protecting both personnel and materials. By understanding their mechanics, key features, and adhering rigorously to safety protocols, facilities can leverage this equipment to optimize workflow, enhance productivity, and maintain a safer working environment. Selecting the right machine for your specific needs and ensuring proper training and maintenance are key to realizing these benefits.
More information: Coil tilter and coil upender