A Side-by-Side Comparison of Leading Steel Coil Packing Line Technologies
- A Side-by-Side Comparison of Leading Steel Coil Packing Line Technologies
- Introduction
- 1. Understanding Steel Coil Packing
- 2. Technology Overview
- 3. Fully Automated Packing Systems
- 4. Key Considerations When Choosing Packing Technology
- 5. Comparative Analysis of Leading Technologies
- 6. Case Studies of Successful Implementations
- 7. The Role of Technology in Safety
- 8. Environmental Considerations
- 9. Future Trends in Steel Coil Packing Technology
- 10. Conclusion
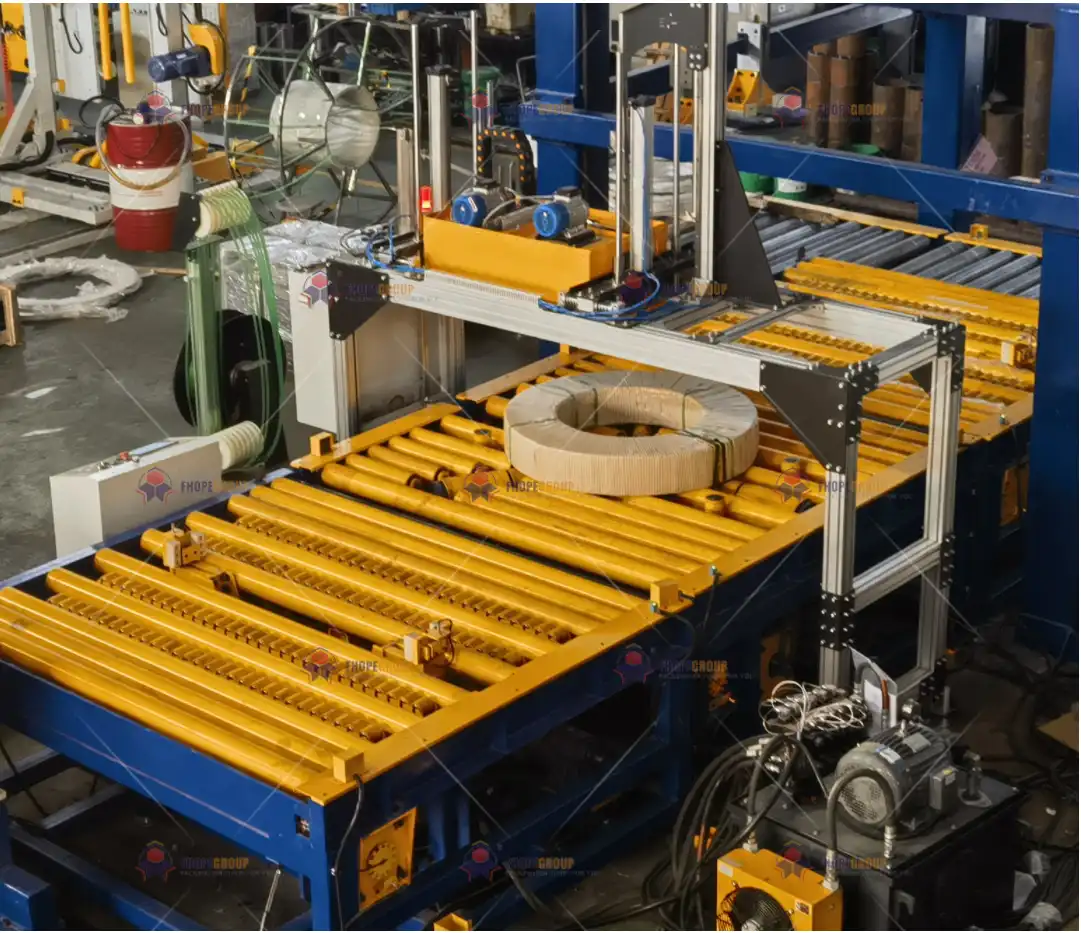
Introduction
In the fast-paced world of manufacturing, efficiency and safety are paramount, especially in the steel industry. One of the critical processes in steel production is the packing of steel coils, which involves various technologies designed to streamline operations while ensuring the integrity of the product. With advancements in technology, manufacturers are presented with a myriad of options to enhance their packing lines. This article aims to provide a comprehensive side-by-side comparison of leading steel coil packing line technologies, helping businesses make informed decisions that align with their operational needs.
In this exploration, we will delve into the unique features, benefits, and drawbacks of each technology. Whether you’re a seasoned professional in the steel industry or a newcomer looking to optimize your operations, understanding these technologies is crucial for improving productivity and reducing costs.
1. Understanding Steel Coil Packing
Before diving into the various technologies available, it’s essential to grasp what steel coil packing entails. Steel coils are rolled sheets of steel that need to be securely packed for transportation and storage. The packing process typically involves wrapping the coils with protective materials and ensuring they are secured on pallets or in containers to prevent damage during transit.
Key Factors in Steel Coil Packing
When evaluating packing technologies, consider the following key factors:
- Safety: Ensuring the safety of the workers and the product is paramount. Technologies should minimize the risk of injury during handling.
- Speed: The efficiency of the packing process directly impacts overall production timelines. Faster systems can lead to significant savings.
- Cost-effectiveness: Balancing initial investment with long-term savings is critical. The right technology should offer a return on investment through enhanced productivity.
- Flexibility: The ability to adapt to different coil sizes and weights without significant downtime is a valuable feature in any packing line.
2. Technology Overview
a. Manual Packing Systems
Manual packing systems involve human operators who handle the packing process. This technology has been widely used in the steel industry due to its simplicity and low initial investment.
Advantages:
- Cost-effective: Lower upfront costs compared to automated systems.
- Flexibility: Workers can adapt quickly to different coil sizes and packing requirements.
- Skill Utilization: Experienced workers can ensure quality packing through their expertise.
Disadvantages:
- Labor-intensive: Requires more personnel, which can lead to higher labor costs over time.
- Inconsistent Quality: Variability in worker performance can lead to inconsistencies in packing quality.
- Safety Risks: Increased risk of injury due to manual handling of heavy materials.
b. Semi-Automated Packing Systems
Semi-automated packing systems combine human labor with machinery, allowing for greater efficiency while still involving operators in the process. This technology utilizes machines to assist with wrapping and securing the coils, reducing the physical burden on workers.
Advantages:
- Increased Speed: Machines can perform repetitive tasks faster than manual labor, enhancing overall productivity.
- Consistent Quality: Automation reduces the variability in packing quality, leading to more uniform results.
- Reduced Labor Costs: While some human involvement is still required, overall labor needs are reduced.
Disadvantages:
- Higher Initial Investment: Semi-automated systems can be more expensive to implement than manual systems.
- Training Requirements: Operators need training to effectively use and maintain the machinery.
- Maintenance Needs: Increased reliance on machinery necessitates regular maintenance and potential downtime.
3. Fully Automated Packing Systems
Fully automated packing systems represent the pinnacle of technology in steel coil packing. These systems utilize advanced robotics and software to handle the entire packing process with minimal human intervention.
Advantages:
- Maximized Efficiency: Automated systems can operate continuously, significantly increasing throughput.
- Precision and Consistency: Robotics ensure precise packing, reducing the risk of damage to coils.
- Lower Long-term Labor Costs: While the initial investment is high, the reduction in labor costs can lead to substantial savings over time.
Disadvantages:
- High Initial Cost: The setup cost for fully automated systems can be prohibitive for smaller manufacturers.
- Complexity: These systems require a skilled workforce for programming, troubleshooting, and maintenance.
- Limited Flexibility: Some automated systems may struggle with non-standard coil sizes or weights without reconfiguration.
4. Key Considerations When Choosing Packing Technology
Selecting the right packing technology for steel coils is not a one-size-fits-all decision. It’s essential to evaluate several factors specific to your operational needs. Here are some key considerations:
a. Production Volume
Understanding your production volume is crucial. High-volume operations may benefit from fully automated systems, while lower volume needs might be adequately served by semi-automated or manual systems. A thorough analysis of your output will help determine the appropriate level of automation.
b. Space and Layout
The physical space available for your packing line can significantly influence your choice of technology. Automated systems often require more floor space and specific layouts to function optimally. Conversely, manual and semi-automated systems may offer greater flexibility in tighter spaces.
c. Integration with Existing Equipment
Consider how the new packing technology will integrate with your current equipment and processes. Seamless integration can enhance overall efficiency, while incompatibilities can lead to operational disruptions. Look for systems that offer easy compatibility with your existing production line.
d. Future Growth and Scalability
As your business grows, so will your packing needs. Choosing technology that allows for scalability ensures that you won’t need to invest in a new system down the line. Consider options that can easily expand in capacity or adapt to new products as your business evolves.
5. Comparative Analysis of Leading Technologies
a. Manual vs. Semi-Automated Systems
When comparing manual and semi-automated systems, consider the trade-offs between cost and efficiency. Manual systems may save on initial costs, but semi-automated systems can significantly enhance speed and consistency, ultimately leading to lower operational costs.
b. Semi-Automated vs. Fully Automated Systems
The debate between semi-automated and fully automated systems often hinges on budget and long-term goals. Semi-automated systems offer a balance of human oversight and machine efficiency, making them suitable for many operations. In contrast, fully automated systems provide the highest throughput but require a larger initial investment.
c. Flexibility vs. Efficiency
Flexibility in packing can be crucial for manufacturers dealing with various coil sizes. While manual and semi-automated systems offer more adaptability, they may sacrifice some efficiency. Conversely, fully automated systems excel in efficiency but can struggle with flexibility unless specifically designed for diverse product lines.
6. Case Studies of Successful Implementations
a. Example 1: A Large Steel Manufacturer
One prominent steel manufacturer transitioned from a manual packing system to a fully automated solution. This shift resulted in a 30% increase in throughput, allowing them to meet rising demand without increasing labor costs. The investment paid off within two years due to the significant reduction in packing time and improved safety records.
b. Example 2: A Mid-sized Production Facility
A mid-sized facility opted for a semi-automated system to balance efficiency and investment. By automating key processes while retaining skilled labor for quality control, they achieved a 25% reduction in packing time and improved product quality. This flexibility allowed them to adapt quickly to changes in demand.
7. The Role of Technology in Safety
As automation becomes more prevalent in the steel industry, safety concerns remain at the forefront. Automated systems can enhance safety by reducing the need for manual handling of heavy materials. However, it’s crucial to ensure that proper safety protocols are in place for both automated and manual systems to minimize risks.
8. Environmental Considerations
In today’s eco-conscious environment, the sustainability of your packing technology should not be overlooked. Fully automated systems often reduce material waste through precise packing, contributing to more sustainable operations. Additionally, manufacturers should consider energy efficiency and the overall carbon footprint of their packing lines.
9. Future Trends in Steel Coil Packing Technology
As technology continues to evolve, several trends are shaping the future of steel coil packing. Smart technology, including IoT integration, is becoming more common, allowing for real-time monitoring and adjustments in packing operations. These advancements promise to enhance efficiency and reduce downtime through predictive maintenance.
10. Conclusion
In conclusion, selecting the right steel coil packing line technology involves careful consideration of various factors, including production volume, space, integration capabilities, and future growth. Each technology—manual, semi-automated, and fully automated—offers distinct advantages and disadvantages that must align with your operational needs. By understanding these differences, manufacturers can make informed decisions that enhance productivity, improve safety, and support sustainable practices.
As the steel industry continues to evolve, staying informed about the latest technologies will be essential for maintaining a competitive edge. Investing in the right packing technology can lead to significant operational improvements, ultimately contributing to long-term success.