Enhancing Logistics Efficiency: An Overview of the A 300 Automatic Pallet Wrapping Machine
Streamlining warehouse operations and ensuring load security during transit are critical challenges in modern logistics. Manual pallet wrapping can be time-consuming, inconsistent, and physically demanding. Automated solutions like the A 300 automatic pallet wrapping machine offer a robust alternative, designed to significantly enhance the efficiency, consistency, and safety of the pallet wrapping process.
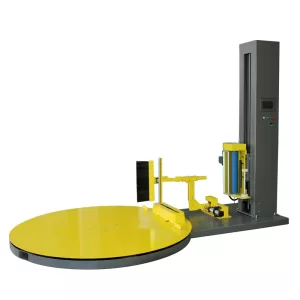
Video showcasing the operation of an automatic pallet wrapping machine.
Understanding the A 300 Automatic Pallet Wrapper
The A 300 is engineered to automate the application of stretch wrap film to goods stacked on pallets. This process secures the load, providing stability and protection against environmental factors and shifting during handling and transportation.
Its core structure typically includes:
- Rotating Turntable: Securely holds and rotates the palletized load.
- Film Carriage System: Moves vertically along a mast, dispensing the stretch film evenly around the load.
- Control System: Often featuring a PLC (Programmable Logic Controller) and touchscreen interface, allowing operators to set parameters like wrap cycles, tension, and film overlap for consistent results across different load types.
The robust construction ensures durability for demanding industrial environments, contributing to optimized workflow and reduced material waste.
Key Specifications and Operational Parameters
These specifications outline the typical capabilities of the A 300 model series.
- Machine Type: Automatic Pallet Stretch Wrapper
- Load Capacity: Typically supports up to 2000 kg (approx. 4400 lbs)
- Max Pallet Dimensions: Accommodates standard pallet sizes (e.g., Length: 1200mm; Width: 1200mm; Height: up to 2400mm)
- Film Type Compatibility: Designed for use with standard stretch film and pre-stretched film varieties.
- Wrapping Efficiency: Capable of processing up to 40 pallets per hour, depending on configuration and wrap settings.
- Power Requirements: Standard configurations often use 220V, 50Hz, single phase (verify based on regional requirements).
- Control Interface: PLC with intuitive touchscreen for easy operation and program adjustments.
- Turntable Speed: Variable, commonly up to 12 revolutions per minute (rpm).
- Film Carriage Speed: Adjustable vertical speed, often up to 5 meters per minute.
- Approximate Machine Footprint: Length: 2600mm; Width: 1500mm; Height: 2500mm (may vary).
- Standard Safety Features: Includes emergency stop buttons and often safety guarding around moving parts.
- Automation Capabilities: Features like automatic load height detection (photocell) and automatic film cut-and-clamp systems enhance efficiency.
- Energy Considerations: Modern designs often incorporate energy-efficient motors and drive systems.
Note: The parameters listed provide a general guide. Specific machine configurations can vary. For exact specifications tailored to your operational needs, direct consultation is recommended.
Core Benefits of Automated Pallet Wrapping
Implementing an automatic pallet wrapper like the A 300 brings several key advantages:
- Increased Efficiency and Throughput: Automation drastically reduces the time required to wrap a pallet compared to manual methods, significantly boosting packaging line throughput.
- Improved Load Stability and Security: Consistent film tension and precise overlap ensure pallets are wrapped securely and uniformly, minimizing product shifting and damage during transit.
- Optimized Material Usage: Precise control over film stretch and application reduces film consumption compared to inconsistent manual wrapping, leading to cost savings.
- Enhanced Worker Safety: Automating the wrapping process eliminates the need for manual stretching and bending, reducing the risk of musculoskeletal injuries for warehouse staff.
Key Industry Applications
The versatility of the A 300 automatic pallet wrapper makes it suitable for a wide range of industries:
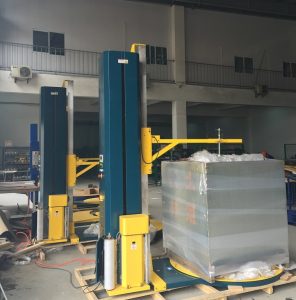
1. Distribution and Logistics Centers: Ensuring Transit Integrity
In high-volume distribution environments, ensuring load stability is paramount. The A 300 provides consistent, tight wrapping that secures goods effectively, reducing the likelihood of damage during shipping and handling, ultimately improving customer satisfaction and lowering return rates.
2. Food and Beverage Sector: Maintaining Product Quality and Hygiene
This industry requires packaging solutions that protect goods from contamination and maintain freshness. The secure wrap provided by the A 300 helps shield products from dust, moisture, and pests while stabilizing multi-unit packs, ensuring compliance with hygiene standards.
3. Chemical and Manufacturing Industries: Prioritizing Safe Handling
For manufacturers dealing with potentially hazardous materials or sensitive components, secure packaging is critical. The A 300 ensures robust containment and stabilization of palletized loads, reducing risks associated with handling and transport, aiding in regulatory compliance, and protecting personnel and the environment.
Considerations for Implementation
When considering an automatic pallet wrapper, factors such as available floor space, power supply adequacy, integration with existing conveyor systems (if applicable), and required throughput capacity should be assessed to ensure the chosen model aligns with operational requirements.
In conclusion, the A 300 automatic pallet wrapping machine represents a valuable investment for businesses seeking to improve packaging efficiency, enhance load security, reduce material costs, and promote workplace safety within their logistics and warehousing operations.