Optimizing Tyre Packaging: Enhancing Efficiency and Branding with Automated Wrapping
The process of packaging tyres presents unique challenges, from ensuring product protection during transit and storage to maintaining handling efficiency and brand consistency. Manual methods can be labor-intensive, inconsistent, and may not provide the necessary level of protection or professional presentation. Automated tyre wrapping machines offer a robust solution to these challenges.
Why Consider Automated Tyre Wrapping Solutions?
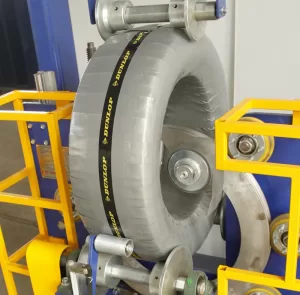
Transitioning from manual to automated tyre packaging yields several operational benefits:
- Increased Efficiency: Automated systems significantly speed up the packaging process compared to manual wrapping.
- Consistent Quality: Machines apply stretch film and branding elements uniformly, ensuring every tyre is packaged to the same standard.
- Improved Protection: A secure wrap protects tyres from dust, moisture, and scuffing during handling and storage.
- Reduced Labor Costs: Automation frees up personnel for other value-added tasks.
- Enhanced Safety: Reduces manual handling and associated ergonomic risks for operators.
Key Components and Functionality of Modern Tyre Wrapping Machines
Understanding the core features helps in appreciating the value these machines bring to the production line.
1. Secure Stretch Film Wrapping
The primary function involves applying layers of stretch film around the tyre.
- Process: A wrapping arm typically moves orbitally around the tyre as it is held and rotated.
- Benefit: This creates a tight, unitized package that contains the tyre securely, offering excellent protection and stability. This method is fundamental in modern industrial packaging equipment.
2. Ergonomic Rotating Ring Design
Many advanced machines utilize a rotating ring structure.
- Functionality: This ring securely holds the tyre while enabling the wrapping action. Crucially, this design often facilitates easier loading and unloading for operators.
- Advantage: Compared to some alternative designs, this can significantly reduce physical strain and improve workflow efficiency. The Fhope tyre wrapping machine incorporates such user-centric design principles.
3. Integrated Logo Tapping for Branding
Beyond simple containment, applying branding directly onto the wrapped tyre is a key feature.
- Mechanism: A dedicated section applies a logo, text, or other identifier onto the stretch film post-wrapping.
- Technology: This typically uses durable hot-melt or solvent-based inks for clear and lasting marks.
- Value: This transforms a protective wrap into a branding opportunity, making tyres shelf-ready and easily identifiable.
4. Control Systems and Customization
Modern machines rely on sophisticated controls for precision and flexibility.
- PLC Control: Programmable Logic Controllers (PLCs) automate and synchronize the wrapping and tapping processes, ensuring reliability and repeatability.
- HMI Interface: A touchscreen Human-Machine Interface (HMI) allows operators to easily select presets, adjust parameters (like wrap count or logo placement), and monitor machine status and production data.
- Adaptability: A significant advantage is the potential for customization. Machines can often be tailored to accommodate specific tyre size ranges or unique operational requirements, ensuring a perfect fit for diverse production needs.
5. Safety and Support
Operational safety and long-term reliability are paramount.
- Safety Measures: Features like physical guards around moving parts and light curtains at entry/exit points are standard for operator protection.
- Ongoing Support: Reputable providers offer after-sales service and support, crucial for maintaining machine uptime and performance throughout its lifecycle.
- Continuous Improvement: Leading manufacturers invest in research and development to continually refine machine design for better efficiency, performance, and user experience.
Selecting the Right Tyre Packaging Solution
Choosing the appropriate machinery involves considering:
- Throughput Requirements: How many tyres need to be wrapped per hour/day?
- Tyre Size Range: What are the minimum and maximum tyre dimensions?
- Level of Automation: Does the entire line need integration?
- Branding Needs: Is logo tapping essential?
- Budget and ROI: Evaluating the long-term value against the initial investment.
Conclusion
Automated tyre wrapping machines represent a significant step forward in optimizing packaging operations within the tyre industry. By combining efficient stretch wrapping, ergonomic design, integrated branding capabilities, and robust control systems, these solutions address key challenges related to protection, speed, consistency, and labour. Investing in the right tyre packaging technology enhances product presentation and delivers substantial improvements in operational efficiency and safety.