6 Key Elements to Creating a Successful Steel Wire Packing Strategy
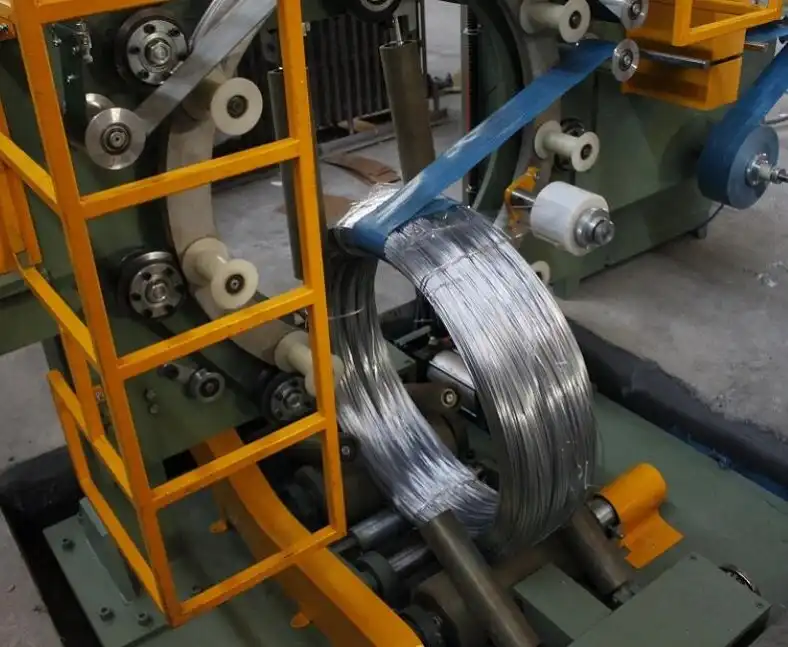
Introduction
Steel wire, used in industries such as construction, manufacturing, and engineering, requires meticulous care during packing to maintain its quality and integrity. Proper packing not only prevents damage but also streamlines transportation and storage, ensuring that the wire is delivered in optimal condition. A successful packing strategy needs to account for the wire’s characteristics, the environmental conditions during transportation, and the cost-effectiveness of materials used. This article discusses six key elements to creating an effective steel wire packing strategy, considering various packaging materials, wire features, and machinery selections.
1. Understanding the Characteristics of Steel Wire
The first step in creating an effective packing strategy is understanding the specific characteristics of the steel wire being packed. Steel wire can vary significantly in terms of its thickness, strength, and finishing, all of which can influence how it should be packed.
- Wire Size and Weight: Steel wire can come in a variety of sizes, ranging from very thin, flexible strands to thick, heavy-duty cables. Thicker wires may require more robust packing materials to provide adequate support, whereas thinner wires are more susceptible to tangling and may need tighter wrapping.
- Surface Finishing: Wires with a galvanized or stainless steel finish have different corrosion resistance properties compared to carbon steel wires. Proper packaging is essential to prevent rusting and maintain the wire’s finish, especially during long-term storage or transport through humid environments.
Tailoring the packaging process to these specific attributes ensures that the wire will arrive at its destination in perfect condition, ready for use.
2. Choosing the Appropriate Packing Materials
Choosing the right packing materials is crucial for protecting steel wire during transportation and storage. The selection of materials depends on factors such as the type of wire, its sensitivity to environmental conditions, and the method of transport.
- Shrink Film: For added protection, shrinking solutions offer a tightly sealed barrier around the steel wire coil, keeping moisture and dust out. This option is particularly beneficial for outdoor storage or long-term warehousing, where the wire might be exposed to harsh elements.
- Stretch Film: This material provides flexibility and is ideal for securing coils during transit. It is often used in conjunction with automated wrapping machines, which can apply the stretch film with consistent tension, ensuring that the wire is tightly bound without over-compressing the coil.
- Paper: Paper serves as a cost-effective solution for providing a protective layer between the coil and the outer packaging. It is particularly useful for minimizing surface scratches during handling and transit. Additionally, paper is biodegradable, making it a more eco-friendly choice.
- Fabric: For heavy-duty protection, fabric materials like woven polyester can be used as a durable barrier around the steel wire. Fabric offers excellent resistance to abrasions and provides cushioning that is beneficial for delicate or high-value wire products.
- Protective Layers: Depending on the wire type, adding foam, cardboard, or plastic between the wire and the outer packing layer can prevent surface scratches or damage caused by impact during transit.
The goal is to select materials that offer the appropriate level of protection while also being cost-effective and easy to apply, ensuring smooth operations.
3. Selecting the Right Packing Machinery
Automating the packing process through the use of specialized machinery is key to achieving consistency and efficiency. The choice of machinery will largely depend on the type of wire being packed and the scale of the operation.
- Automatic Wrapping Machines: These machines are essential for high-volume production lines. They can wrap coils of steel wire using stretch or shrink film, ensuring a tight and secure wrap that reduces the risk of damage during transportation. Automated systems also allow for precise control over the amount of material used, ensuring cost-effectiveness by reducing waste.
- Coil Strapping Machines: For heavier wire coils, a coil strapping machine can be an excellent solution. These machines apply durable straps that hold the coil in place during transport. Strapping adds an extra layer of security, preventing the coils from shifting or becoming loose during movement.
- Custom Solutions: In some cases, a custom-built packing system may be the best option. These systems are designed to handle coils of varying sizes and can combine multiple packaging techniques—such as wrapping and strapping—into a single streamlined process. Custom solutions often include adjustments for coil size, material type, and packing speed, allowing for greater flexibility and productivity.
Selecting the right packing machinery ensures that the steel wire is packed consistently and efficiently, reducing labor costs and ensuring product quality.
4. Adapting to Environmental Conditions
Another key factor in the steel wire packing process is accounting for the environmental conditions the wire will face during transportation and storage. Steel wire is particularly susceptible to corrosion, and external conditions such as humidity, temperature fluctuations, and UV exposure can have a significant impact on the quality of the product.
- Moisture Resistance: If the steel wire is being transported or stored in humid environments, the packaging must protect it from moisture. Using VCI (Vapor Corrosion Inhibitor) film or other moisture-resistant materials can prevent rust and corrosion from forming on the wire’s surface.
- UV Protection: For outdoor storage or transportation through sunny regions, UV-resistant films should be used to prevent degradation caused by exposure to sunlight. Over time, UV rays can weaken some packaging materials and damage the surface of the steel wire.
- Temperature Control: Extreme temperatures can cause expansion and contraction of both the wire and the packing materials, potentially compromising the integrity of the packaging. Choosing materials that are flexible and durable under a wide range of temperatures can help mitigate this risk.
By adjusting your packing strategy based on environmental factors, you ensure that the steel wire remains protected throughout its journey, regardless of external conditions.
5. Securing Steel Wire for Safe Transportation
Transportation is one of the most critical phases in the steel wire packing process. During this stage, the wire is subjected to movement, vibrations, and potential impacts, which can lead to damage if it is not properly secured. Ensuring that the steel wire remains stable and protected during transit is essential for maintaining product quality and avoiding costly returns.
- Load Locking Techniques: One of the most effective ways to secure the steel wire coil is by using a combination of wrapping and strapping. Wrapping the coil tightly with stretch film ensures that the wire stays in place, while strapping provides an additional layer of stability. These methods prevent the coil from shifting during transit, which could otherwise lead to damage or deformation.
- Shock Absorption: Adding foam or other cushioning materials around the coil is another effective way to prevent damage during transportation. Shock-absorbing materials help to mitigate the impact caused by rough handling, bumps, or sudden stops. This is particularly important for fragile or thinner wire coils that are more susceptible to bending or surface damage.
- Using Proper Machinery: Machines designed for securing loads, such as coil strapping machines or automatic wrapping systems, can apply consistent tension to ensure the steel wire is tightly secured. These machines can also help automate the load securing process, reducing labor and increasing efficiency.
By implementing effective load securing techniques, companies can reduce the risk of product damage during transportation and ensure that the steel wire reaches its destination in the best possible condition.
6. Balancing Cost and Efficiency
While the primary goal of a steel wire packing strategy is to protect the product, it’s also essential to consider the overall cost and efficiency of the packing process. Overpacking can lead to excessive material use and higher costs, while underpacking could result in damaged goods and customer dissatisfaction. Finding the right balance between cost and effectiveness is key to maintaining profitability while ensuring product safety.
- Material Optimization: Using high-quality materials that offer adequate protection without being overused is one of the most effective ways to control costs. Automated packing machines can be programmed to apply just the right amount of wrapping or strapping to each coil, reducing material waste. This ensures that the wire is well-protected without incurring unnecessary expenses.
- Reusable Packing Materials: For companies that frequently transport steel wire between the same locations, using reusable packing materials such as heavy-duty plastic or metal supports can help reduce long-term costs. These materials can be used multiple times, making them a cost-effective option for repeated shipments.
- Labor Efficiency: Automating the packing process can significantly reduce labor costs by minimizing the need for manual handling. Automated machines can wrap and secure the coils quickly and consistently, freeing up workers to focus on other tasks and improving overall operational efficiency.
Balancing cost and efficiency ensures that the steel wire packing process remains financially sustainable while still delivering high-quality protection for the product.
Conclusion
Creating a successful steel wire packing strategy involves more than just selecting the right materials or machinery—it requires a holistic approach that takes into account the specific characteristics of the wire, the environmental conditions it will face, and the overall cost-efficiency of the process. By understanding the unique requirements of steel wire, choosing the right packaging materials, and investing in appropriate machinery, companies can ensure that their products remain safe, secure, and ready for use upon delivery.
Incorporating these six key elements into your packing strategy will not only enhance the protection of your steel wire but also improve the efficiency and cost-effectiveness of your entire operation.