2024 Automation Trends and Developments in Steel Coil Packaging
- 2024 Automation Trends and Developments in Steel Coil Packaging
- The Role of Automation in Steel Coil Packaging
- Top Automation Trends in 2024
- 1. Robotic Integration in Packaging Processes
- 2. Artificial Intelligence and Machine Learning
- 3. Internet of Things (IoT) Integration
- 4. Automated Quality Control Systems
- 5. Sustainability and Green Packaging Solutions
- 6. Collaborative Robots (Cobots)
- 7. Advanced Wrapping Technologies
- 8. Integration of Digital Twins
- 9. End-to-End Automation Solutions
- 10. Cybersecurity in Automated Systems
- Benefits of Automation in Steel Coil Packaging
- Challenges of Automation in Steel Coil Packaging
- Future Outlook for Steel Coil Packaging Automation
- Conclusion
As automation continues to transform industries worldwide, the steel coil packaging sector is no exception. In recent years, automation has been pivotal in enhancing the efficiency, safety, and sustainability of this industry. Steel coil packaging has evolved significantly with the implementation of advanced technologies and automation processes, which have drastically reduced manual labor, minimized human error, and increased overall production capacity. As we move into 2024, the landscape of automation in steel coil packaging is set to change even further, with exciting new trends and developments on the horizon.
In this article, we will dive deep into the latest automation trends in steel coil packaging, explore the role of robotics, AI, and IoT, and discuss how these innovations are shaping the future of the industry.
The Role of Automation in Steel Coil Packaging
The steel coil packaging process involves wrapping steel coils in protective materials such as paper, plastic, or metal to prevent corrosion and damage during transportation and storage. Traditionally, this was a highly manual process that involved multiple steps and significant labor. With the introduction of automation, this process has become faster, more consistent, and safer.
Automation in steel coil packaging encompasses everything from automated wrapping machines to robotic arms that handle the steel coils with precision. These systems not only improve productivity but also reduce the risk of workplace injuries, a critical concern in industrial environments. For instance, systems like the automatic coil down-ender and strapping machines have eliminated many manual tasks, offering consistent performance with minimal human intervention.
Top Automation Trends in 2024
1. Robotic Integration in Packaging Processes
One of the most significant trends in 2024 is the increasing use of robotics in steel coil packaging. Robotic arms equipped with sensors and AI-driven control systems are taking over many tasks that were previously done manually. These robots are capable of lifting, rotating, and wrapping steel coils with extreme precision. For example, the turnstile systems integrated with robotic arms efficiently handle multiple coils at once, increasing throughput while reducing the need for human operators. The use of robotics has led to higher throughput, reduced labor costs, and more consistent packaging quality.

2. Artificial Intelligence and Machine Learning
Incorporating AI and machine learning into packaging systems is revolutionizing the steel coil packaging process. AI systems can analyze data from sensors to optimize the packaging process, predict potential breakdowns, and recommend preventive maintenance measures. This predictive maintenance reduces downtime and improves overall equipment efficiency (OEE). Furthermore, machine learning algorithms can learn from past packaging operations, making them more efficient over time.
3. Internet of Things (IoT) Integration
Another key trend is the integration of the Internet of Things (IoT) into steel coil packaging systems. IoT-enabled devices can collect real-time data from machines and equipment, allowing for better monitoring and control of the packaging process. With IoT, manufacturers can gain valuable insights into equipment performance, track the status of steel coils during packaging, and optimize the entire supply chain. The integration of MES/ERP systems further connects data across production lines, enhancing overall operational efficiency.

4. Automated Quality Control Systems
In 2024, automated quality control systems will become more prevalent in steel coil packaging. These systems use cameras, sensors, and AI-driven software to inspect the quality of the packaging in real time. Any defects or inconsistencies can be identified and rectified immediately, ensuring that the steel coils are properly protected. This not only reduces waste but also enhances the overall quality of the packaging. Systems like sensor-based encoders for measuring coil dimensions ensure precision in packaging.
5. Sustainability and Green Packaging Solutions
As environmental concerns continue to grow, sustainability in steel coil packaging is becoming a top priority. Automation is playing a significant role in promoting green packaging solutions. Automated systems are being designed to minimize material waste, use eco-friendly packaging materials, and reduce energy consumption. For instance, automated coil wrapping machines are optimized to use less material without compromising the protection of the coils. In 2024, we expect to see more companies adopting sustainable automation solutions that align with their environmental goals.
6. Collaborative Robots (Cobots)
Collaborative robots, or cobots, are designed to work alongside human operators in the packaging process. These robots are equipped with advanced safety features, allowing them to safely interact with humans on the production floor. Cobots are particularly useful in tasks that require a combination of human judgment and robotic precision, such as final quality checks and material handling. In 2024, we anticipate a rise in the adoption of cobots in the steel coil packaging industry.
7. Advanced Wrapping Technologies
Advanced wrapping technologies are gaining traction as automation continues to evolve. New wrapping machines equipped with smart technology can adjust the tension, speed, and type of wrapping material used based on the specific needs of each steel coil. These machines ensure that the coils are wrapped tightly and securely, reducing the risk of damage during transportation.
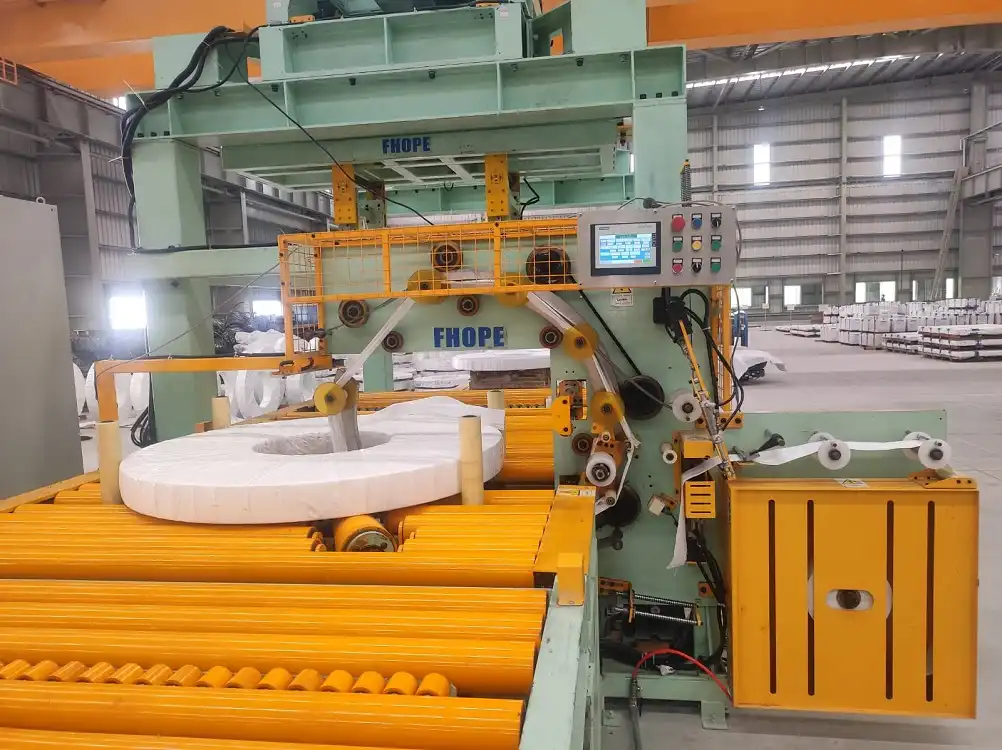
8. Integration of Digital Twins
In 2024, digital twin technology is set to make a significant impact on steel coil packaging operations. A digital twin is a virtual replica of physical systems, such as packaging lines or entire production environments. This technology allows manufacturers to simulate, monitor, and optimize their packaging processes in real-time without interrupting actual production. By creating a digital model of the steel coil packaging line, manufacturers can detect potential issues, identify bottlenecks, and test new strategies for efficiency improvements before implementing them in the physical environment.
Digital twins also play a key role in predictive maintenance by analyzing data from IoT-enabled sensors and machine logs. This helps manufacturers predict machine failures, schedule maintenance more effectively, and ultimately minimize downtime. In addition, digital twins help optimize machine performance and packaging accuracy, ensuring that steel coils are handled with care and protected adequately during transport and storage.
9. End-to-End Automation Solutions
End-to-end automation refers to the automation of the entire packaging process, from material handling and wrapping to quality control and labeling. In 2024, more companies are expected to adopt comprehensive automation solutions that streamline every step of the steel coil packaging workflow. These systems integrate various automated machines—such as coil turnstiles, down-enders, wrapping machines, and strapping machines—to ensure a seamless transition from one stage to another.
By eliminating manual interventions, end-to-end automation reduces the risk of human error, enhances consistency, and speeds up production. For example, an automated coil turnstile can position multiple coils for wrapping or strapping without requiring manual handling, while an automated strapping machine ensures precise and secure packaging with PET or steel belts, reducing the likelihood of coil damage during transport. These comprehensive solutions also integrate with MES/ERP systems, providing real-time data on production performance, packaging quality, and inventory management.

10. Cybersecurity in Automated Systems
As automation systems become more connected, the risk of cybersecurity threats also rises. With more packaging machines integrated with IoT, PLCs, and cloud-based monitoring systems, the potential for cyberattacks on these connected devices increases. In 2024, we will see a heightened focus on implementing cybersecurity protocols to protect these automated systems from cyber threats.
Steel coil packaging lines are not only handling sensitive production data but are also linked to larger supply chain systems. A cyberattack on these systems could disrupt production, delay shipments, and compromise the integrity of both the packaging and the product. Advanced encryption techniques, firewalls, and real-time monitoring will be critical in ensuring the security of automated systems.
Benefits of Automation in Steel Coil Packaging
The adoption of automation in steel coil packaging brings numerous benefits that go beyond just improving operational efficiency. Here are some of the most important advantages:
- Increased Efficiency: Automated systems streamline the entire packaging process, reducing the time it takes to wrap, strap, and handle steel coils.
- Cost Savings: By reducing the need for manual labor and minimizing errors, automation significantly lowers operational costs. Additionally, the reduction in material waste due to precise control over wrapping and strapping also leads to savings.
- Improved Safety: Automated systems remove the need for workers to engage in potentially dangerous tasks, such as handling heavy steel coils. This minimizes the risk of workplace injuries and promotes a safer working environment.
- Consistency and Quality: Automation ensures that steel coils are consistently wrapped and strapped with the same level of precision, improving the overall quality of packaging. Automated quality control systems further ensure that any defects are detected and corrected in real time.
- Data-Driven Insights: With IoT, AI, and data integration, manufacturers have access to real-time data that can help optimize the packaging process, predict maintenance needs, and improve decision-making.
Challenges of Automation in Steel Coil Packaging
While automation offers significant benefits, there are also challenges that companies must navigate when implementing automated systems in steel coil packaging:
- High Initial Costs: The upfront investment required for purchasing and installing automated machinery can be substantial. This includes the cost of equipment, software, and training personnel to operate and maintain the new systems.
- Integration with Existing Systems: For factories with older, legacy equipment, integrating new automated systems can be complex. This may require retrofitting older machines or even replacing parts of the production line to ensure compatibility.
- Maintenance and Downtime: Automated systems require regular maintenance to ensure optimal performance. Unplanned downtime due to equipment failures can result in production delays, so it’s important to have a preventive maintenance strategy in place to minimize disruptions.
Future Outlook for Steel Coil Packaging Automation
Looking ahead, the future of steel coil packaging automation is bright. As technology continues to evolve, we can expect further innovations that will enhance efficiency, reduce costs, and improve sustainability. The rise of AI, IoT, robotics, and green technologies will continue to shape the industry, creating a more streamlined and eco-friendly approach to packaging.
One area of particular interest is the development of autonomous packaging systems that require little to no human intervention. As AI and machine learning continue to advance, these systems will become more adaptive, capable of learning from past operations and improving their performance over time. Robotics will also continue to evolve, with faster, more precise machines being developed for handling coils of all sizes and weights.
Sustainability will remain a key focus as manufacturers look for ways to reduce their environmental footprint. The adoption of biodegradable packaging materials, energy-efficient machinery, and recycling programs will be essential for companies looking to meet environmental goals and regulatory requirements.
Conclusion
The year 2024 marks a significant turning point for automation in the steel coil packaging industry. With the integration of robotics, AI, IoT, and sustainability-driven innovations, the industry is set for remarkable growth and transformation. Automation offers unparalleled benefits in terms of efficiency, safety, and cost savings, making it an essential investment for companies in the steel coil packaging sector.