How Are Pallet Flippers Applied in Supply Chain Management?
I saw a facility that struggled to turn pallets quickly. Workers spent hours manually rotating products. This created stress, wasted time, and cut efficiency in half.
Pallet flippers solve this by handling rotation tasks that once required multiple workers. They use controlled rotation to protect goods. They save labor and raise speed. They also cut product damage. They help me reduce strain on my workforce.
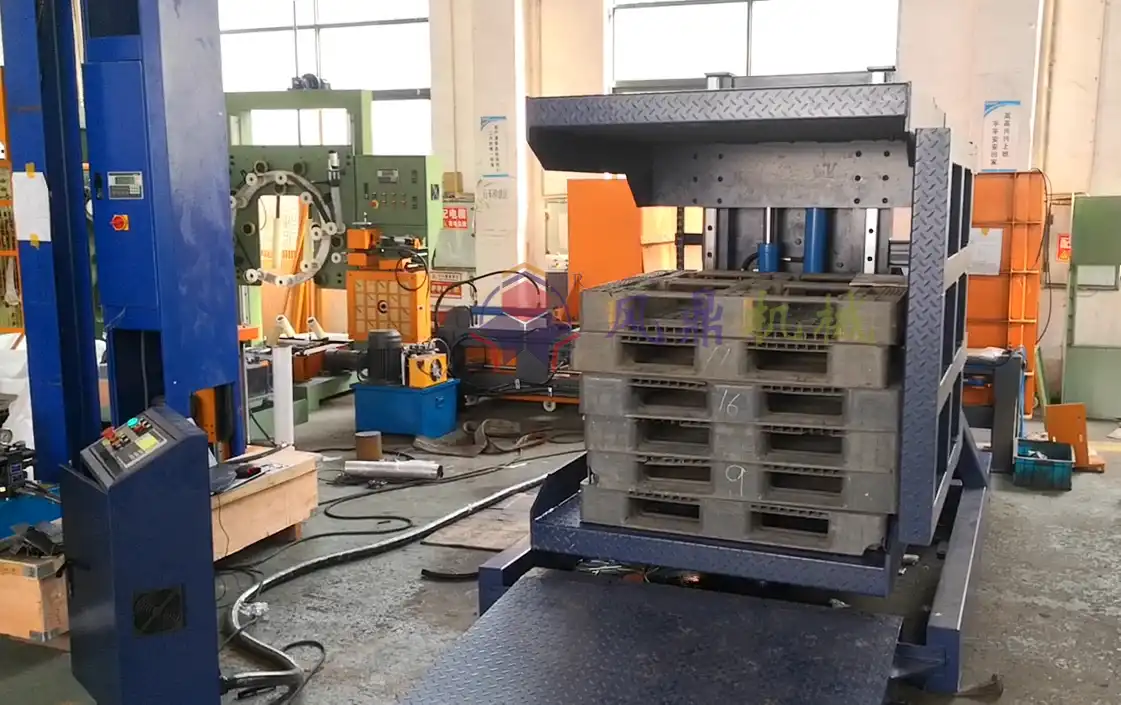
I learned about pallet flippers after I founded FHOPEPACK. I helped clients package steel coils, furniture, and other bulky loads. I saw them worry about wasted time when flipping loads by hand. I introduced pallet flippers to reduce injuries and keep operations smooth. Now I use that same knowledge to explain how they fit into modern supply chains.
How Can Pallet Flippers Improve Efficiency in Supply Chain Operations?
I remember days when I had to rearrange loads on shipping pallets using basic tools. I struggled with repetitive tasks. I wasted hours. I took many breaks because it was exhausting.
Pallet flippers turn these manual struggles into streamlined processes. They grip pallets tightly, rotate them, and allow for quick reorientation. This keeps the workflow on track and ensures smooth operations. This also helps me stick to tight shipment deadlines and prevents shipping mistakes.
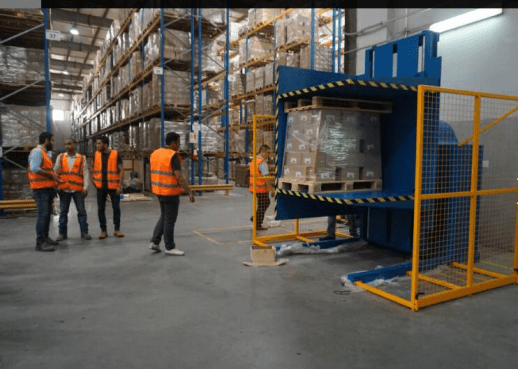
Identifying Operational Bottlenecks
I see big slowdowns when we need to switch pallets with different loading directions. Workers often must rearrange cargo or remove entire loads to correct orientation. That leads to higher labor costs and frustration. It also raises the risk of errors.
I think about the main issues that occur without pallet flippers:
- Manual Handling: Workers lift and rotate heavy pallets by hand. This causes potential injuries, fatigue, and mistakes.
- Damaged Goods: Manual flipping can shift loads. Items can fall or collide. That can harm the contents.
- Time Delays: Manual rotation and repositioning take a long time. It prevents fast dispatch.
- Workflow Breaks: Whenever we change orientation, we stop the entire line, which cuts total output.
When I introduced pallet flippers, I noticed these delays shrink. The machine quickly flips loads. The same tasks that took many people now need one operator. This switch reduces fatigue and speed issues.
I also learned that pallet flippers fit well with automation. They integrate with conveyor lines, wrappers, and forklift systems. This synergy drives continuous loading and unloading. That helps me ship goods faster.
Below is a brief table showing how pallet flippers enhance efficiency:
Operational Factor | Without Pallet Flipper | With Pallet Flipper |
---|---|---|
Labor Required | High | Reduced |
Time to Flip Pallet | Long | Short |
Risk of Product Damage | High | Reduced |
Workflow Disruptions | Frequent | Minimal |
I like to combine pallet flippers with coil wrapping machines and other packaging systems. This helps me handle diverse product types. It lets me keep an eye on each stage of handling. It also allows me to fine-tune the pace of production. This synergy is why I see big benefits in day-to-day operations.
I have seen my clients adopt these flippers to improve speed. One client, who managed big rolls of paper for printing, saved hours per day. He now moves more inventory with fewer accidents. He told me the flipper helped him stay competitive in a tough market. I believe that is the power of automation. I have also learned that making small changes in orientation helps avoid confusion for forklift drivers. They see consistent pallet positioning, so they do not need to guess angles. This leads to fewer forklift collisions and lower upkeep costs.
I feel confident that pallet flippers are a key solution for supply chain efficiency. They help me cut down on wasted time, reduce worker strain, and keep everything organized. They turn an old, labor-heavy process into a seamless action that supports higher throughput and better performance.
What Role Do Pallet Flippers Play in Reducing Labor Costs?
I recall seeing large crews move heavy stacks of materials. They had to realign pallets multiple times a day. They were tired, and the company’s labor costs rose.
Pallet flippers simplify these tasks. They reduce the number of workers needed. They automate flipping and help me avoid overtime. They keep labor expenses low. They also minimize the chance of strain injuries.
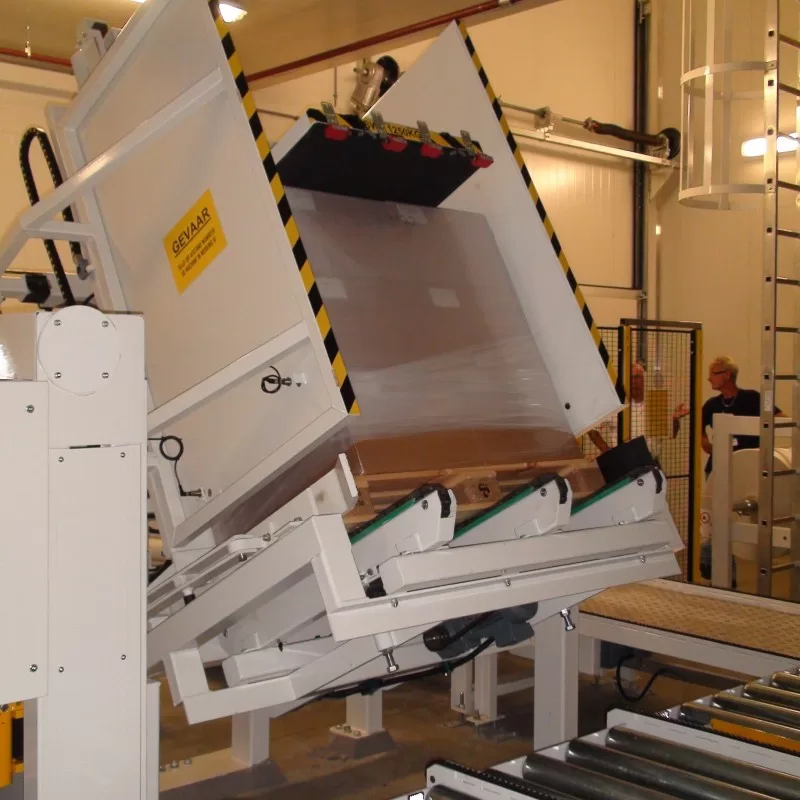
Examining Cost Reduction Strategies
I observe how labor costs shift when I use pallet flippers. I analyze the core factors:
- Fewer Workers: One operator can flip multiple pallets. This frees others for more important tasks.
- Reduced Injury Claims: Manual flipping often causes back or arm strains. Workers can drop loads. A pallet flipper takes away that risk.
- Decreased Training Time: Training an operator on a pallet flipper is quick. Training many workers to handle manual flipping is harder.
- Less Overtime: Automated flipping completes tasks in less time. Workers avoid late hours.
I see these points help a company lower the overall labor cost. Below is a table that shows how much labor cost changes before and after using a pallet flipper:
Labor Metric | Without Pallet Flipper | With Pallet Flipper |
---|---|---|
Number of Workers Needed | Usually higher | Lower |
Injury-Related Costs | Higher | Reduced |
Overtime Requirements | Frequent | Minimal |
Training Time | Longer | Shorter |
A few years ago, I worked with a factory that packed steel coils for export. They needed a large crew to manage orientation changes. They tried to rotate the coils on the pallet by hand. This was risky. They also had more injuries. I introduced them to a pallet flipper. They reduced their manual flipping staff. They reassigned those people to quality control and forklift duties. This new approach cut overhead. It also boosted morale. Workers felt safer and less exhausted.
I prefer to combine pallet flippers with other automation devices. For example, I place a pallet inverting station close to a conveyor. Workers load the pallet onto the conveyor. The pallet flipper inverts it quickly. The newly oriented load moves on to the wrapping station. This arrangement means the line is faster. This helps me avoid paying extra wages to multiple laborers.
Companies that switch to pallet flippers see the largest cost drop when they integrate them across multiple lines. Doing so standardizes flipping processes. It removes random stops. It also simplifies scheduling. In busy seasons, they do not need to hire as many temporary workers. The flipper handles the higher volume. This is a practical way to plan long-term budget strategies.
I share my personal story because I started small. I was short-staffed. I saw that automated flipping reduced my worry about training new hires. It also reduced the time needed to move heavy loads. It gave me more room to focus on other manufacturing processes, like coil wrapping or pallet stretch wrapping. That is how I ended up refining my entire packaging line. Pallet flippers became a valuable part of my toolbox.
How Do Pallet Flippers Ensure Product Safety in Material Handling?
I once saw a facility where broken goods piled up. Workers struggled to flip pallets and accidentally dropped boxes. The broken goods added to losses. Managers had to invest in more robust packaging. It was a never-ending cycle of damages.
Pallet flippers solve that by applying consistent, even pressure when flipping. They keep items in place. They protect loads from sudden shifts. They help me avoid costly replacements or product returns.
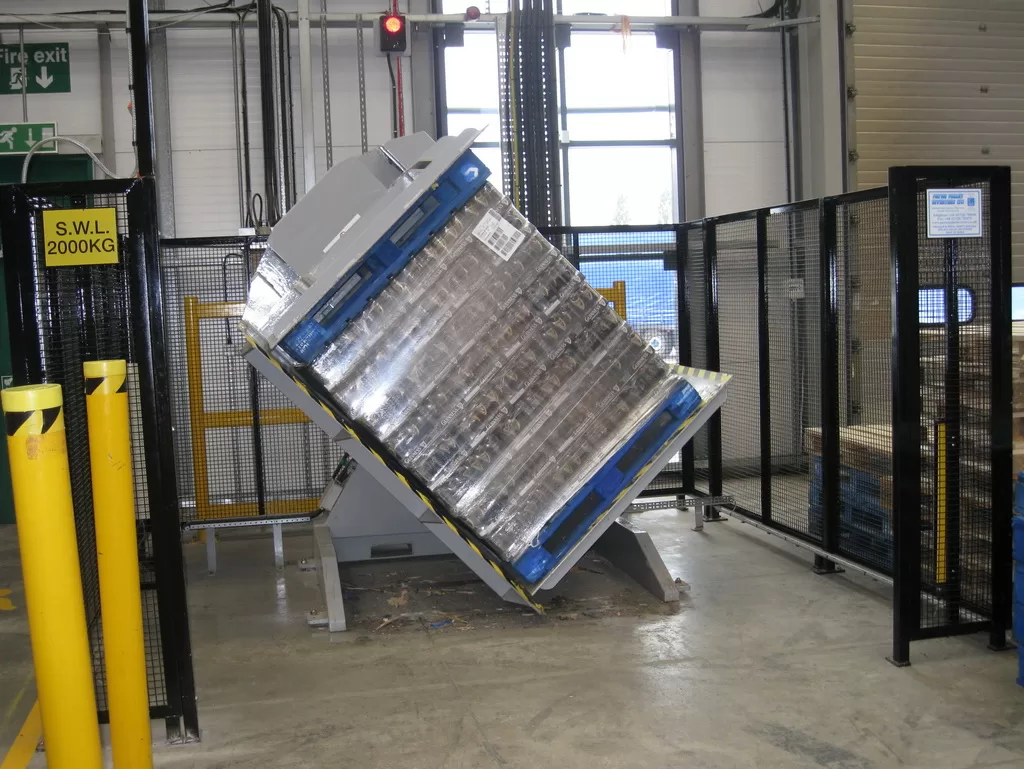
Investigating Safety Protocols
I analyze the direct safety benefits of pallet flippers:
- Secure Grip: The clamps hold the pallet from multiple sides. The goods do not slip. The rotation is smooth.
- Controlled Rotation Speed: The flipper rotates at a steady speed. This avoids abrupt motions. This stops sudden shifts in load weight.
- Reduced Contact: Workers do not need to push or pull the load manually. They keep a safe distance from potential hazards.
- Less Frequent Re-stacking: The flipper positions the goods precisely. Workers do not need to re-stack items after flipping. That means fewer chances for collisions.
I remember an incident that highlighted the importance of safety. A customer used to stack steel coils in a hurry. He asked his team to rotate and re-orient them by hand. One day, a coil rolled off the pallet. It was heavy. It injured a nearby worker and damaged the floor. That led me to introduce a pallet flipper. The coil remained stable throughout the flip. This prevented more accidents and kept the facility safer.
Here is a table that shows how product safety measures compare with and without a flipper:
Safety Aspect | Without Pallet Flipper | With Pallet Flipper |
---|---|---|
Load Stability | Often shaky | Always firm |
Risk of Workplace Injury | High | Low |
Goods Damage Rate | Frequently high | Greatly reduced |
Likelihood of Spills | Common | Unlikely |
I also find it helpful to combine pallet flippers with protective packaging. For instance, I wrap materials with stretch film, then use the flipper to re-orient the load. This synergy prevents items from shifting mid-rotation. It also makes the entire process seamless. Since I run FHOPEPACK, I pay close attention to how different automation systems link together. I see that synergy is key for maximum safety.
Customers sometimes worry about fragile goods. They think flipping might break them. I explain that modern pallet flippers have adjustable grips. They let me set the right pressure and flipping speed. This means delicate items face less stress than they would with manual flipping. With manual flipping, people might handle them roughly to move fast.
I use pallet flippers to maintain a neat, well-managed warehouse. I find that clear labeling and orientation help forklift drivers see which way to pick up loads. That is another safety feature. There is less guesswork. Drivers do not need to spin or swirl heavy goods around.
I think of product safety as more than just preventing breakage. It also includes ensuring a hazard-free environment for workers. A pallet flipper keeps people away from direct contact with heavy products. This means fewer injuries. A flipper is not just about convenience. It is a safeguard for every stage of material handling.
Conclusion
I see pallet flippers as a smart investment for any supply chain. They help me speed up operations, cut labor costs, and protect goods. They support safe handling and let me focus on bigger goals.